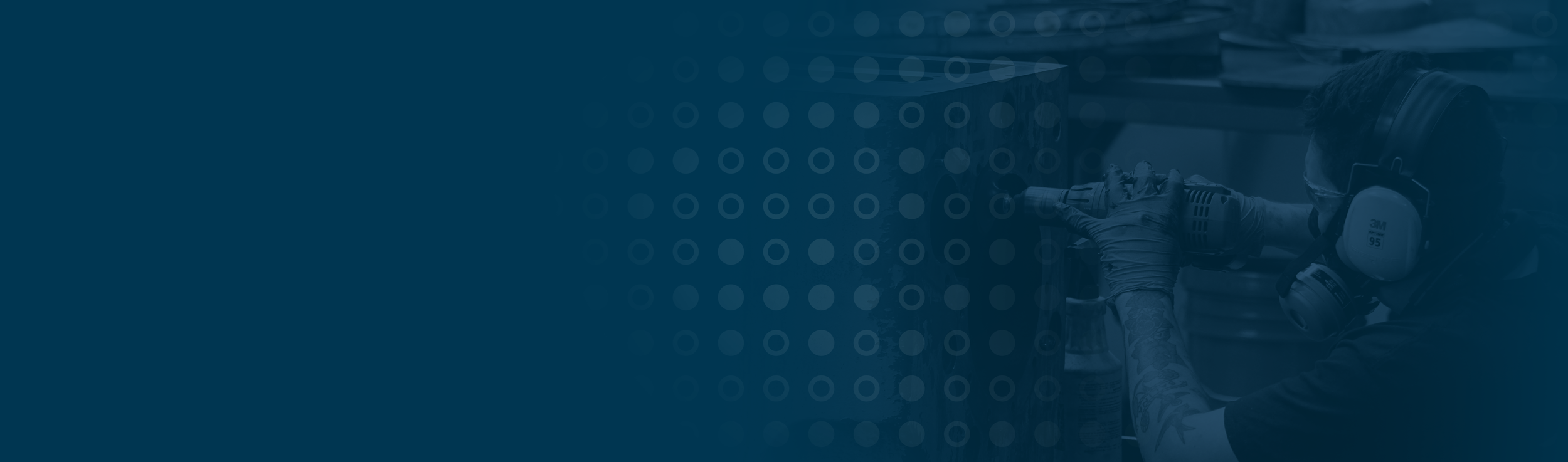
OUR PROCESS
Our Process
All of our vacuum pump technicians follow strict guidelines when servicing our customers' vacuum pump equipment. The procedures outlined below not only ensure a quality rebuild, but ultimate customer satisfaction!
Evaluation
Once a vacuum pump enters an IVS facility, it is visually inspected and photographed for reference. An internal Work Order is generated by a member of our team, and entered into our computer database.
The equipment is then transferred to our tear down area and queued for complete disassembly and decontamination. Once queued, the equipment receives a comprehensive visual and mechanical analysis to ensure conformity to OEM specifications.
All components required to bring the pump back to OEM standards are listed on the Work Order.
Testing
Once service is completed, the equipment is moved to our test station and put through a series of industry-proven tests including base pressure, ballast pressure, and load testing.
Turbomolecular pump testing includes a vibration analysis, speed analysis, and decibel readings, as well as load testing.
This series of tests ensures our customer receives a quality product.
Customer Review
Once evaluation is complete, the Work Order is then reviewed by our Service Manager, and a Service Analysis Form (SAF) is generated and sent to the customer for review.
The SAF provides the customer with a detailed evaluation of the equipment, including cause of failure, parts required for service, and a cost breakdown.
Customers are then given the opportunity to ask additional questions, and for IVS to make any necessary recommendations. One of our Customer Service Representatives will follow up with a phone call to discuss the status of your equipment and gain approval to start the service process.
Shipping
Once the equipment passes all testing, it is prepped for return shipment to our customer.
The oil is drained, the exterior finish of the equipment restored to OEM colors, and returned to your facility.
Smaller pieces of equipment are properly foam packaged prior to shipment.
Service
Once customer approval is given, the Service Manager will issue the components required for service, and assign the job to one of our highly-skilled service technicians.
Components required for industrial vacuum equipment service may include the following consumable items such as Seals, Gaskets, O-Rings, Bearings, Valves, etc. Components required for turbomolecular pumps may include Ceramic Bearings, O-Rings, Vibration Rings, etc.
The assigned service technician is responsible for the cleaning and service of the equipment.
Warranty
IVS prides itself as the industry leader in vacuum pump repair, rebuild and maintenance.
Our industry-leading warranty covers both the workmanship and parts we use in the rebuild process. Our warranty begins from the documented date of installation, not when the unit ships, like OEM’s and other third party pump rebuilders.
Visit the IVS Warranty page to read the policy in full and/or to submit a request for warranty.

Connect With Us on LinkedIn
We’re not all Sales and Service! Follow our company page on LinkedIn and connect with your favorite staff. Stay informed of what’s happening around our business, and the wider vacuum solutions market.
We hope to see you there!